エアリークテスターの技術資料5
エアリークテスター・技術資料
◆ 技術資料 P.5
5.体積と感度の関係
① エアリークテスタにおける体積と圧力変化の理論式 ② 差圧検出器の検出変位が感度に及ぼす影響 ③ Hyper2000の内部体積 ④ 外部容積(検査ワークと配管)の測定方法 ⑤ 体積の違いと感度の比較
6.検出圧力とリーク量
① 検出圧力とリーク量の理論式 ② 検査圧力と感度の関係
◆ 印刷物として御利用になりたい方は、〔お問合せフォーマット〕を通じて、または当社の営業に直接請求して下さい。
◆お詫び 理論式や説明文中、不明な表現があることをお許しください。たとえば、
1.1.2×10-5 → 10のマイナス5乗 2.m3 → mの3乗= 立方メートル 3.大気圧 1.013×105 → 10の5乗
5.体積と感度の関係
差圧変換器、配管、検査ワーク、マスターチャンバーなどを含めた体積を求める方法を理論的に説明します。
① エアリークテスタにおける体積と圧力変化の理論式
A室を検査ワークを含む全体積とし、B室をマスターを含む全体積とします。この時、検査ワーク側に図のような体積変化強制的に与えたとし、各記号を次のように定めます。
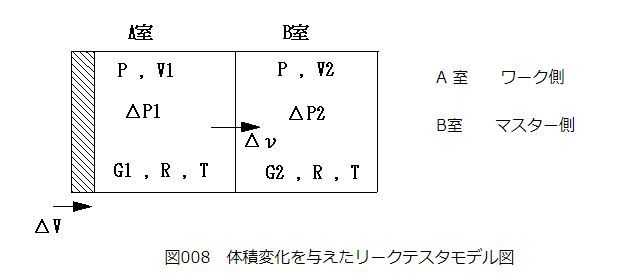
A室とB室の圧力は等しいと仮定する。
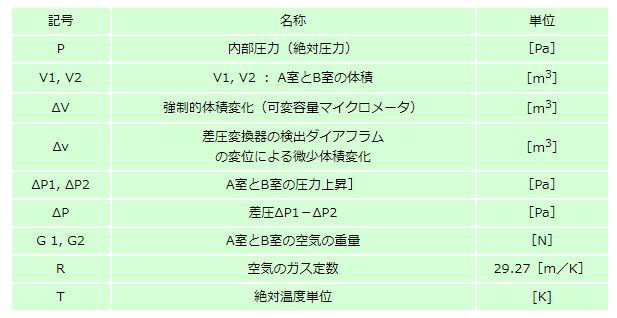
今後使用する記号

A室は、測定器内部体積、外部の配管と検査ワーク体積等の合計体積 V1 を持ち、可変容量マイクロメータの前進により、-ΔV の体積変化が与えられたとする。この時、圧力上昇 ΔP1 が発生し、差圧変換器の金属ダイアフラム変位により体積増加 Δν がある。一方B室は圧力変換器の変位により、体積の変化 -Δν 受け、同時に圧力上昇 ΔP2 が発生する。
圧力変換器の出力はΔP=ΔP1-ΔP2により発生するものとする。状態変化は極めて微小な圧力変化である為、等温変化を仮定する。
初期状態式
A室 PV1 = G1RT-------------------------------------- (2)
B室 PV2 = G2RT-------------------------------------- (3)
変化後の状態式
A室(P+ΔP1)(V1-ΔV+Δν)= G1RT------------- (4)
B室(P+ΔP2)(V2-Δν)=G2RT-------------- (5)
その他の関係式
ΔP = ΔP1-ΔP2---------------------------- (6)
k = V1/V2 = G1/G2---------------------------- (7)
(2)~(7)式より高次の項を省略して整理すると、
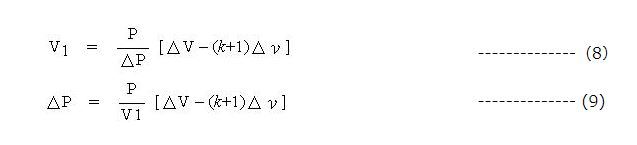
(8)、(9)式が導出されます。
② 差圧検出器の検出変位が感度に及ぼす影響
次にΔνについて考えてみよう。差圧変換器は圧力変化によって発生する変位を磁気変化として検出し、差圧を電気信号に変換します。従って、必ず体積の変化が発生します。体積変化が大きい程、ある体積内の体積変動による圧力測定において、変換器の機械的感度が低下します。その代表的なものは水柱マノメーターのようなものであり、管内径をΦ8とすると、10[Pa]の変化に対して約0.05[cc]にもなります。
(9)式において仮にk ≒ 1とすると、強制的体積変化ΔVに対するΔνが大きくなると、差圧ΔPが減少する、すなわち感度が低下することがわかる。ここで、

と定義すると、(8), (9)式は
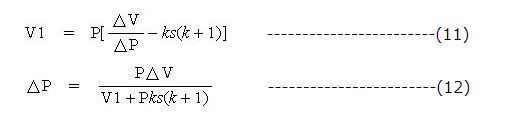
となる。ここで、Hyper2000エアリークテスターに使用している差圧変換器DP-200は、

です。前機種 Hyper1000 の単位圧力あたりの変位は ks=0.9×10-4 [cc/mmH2O] であったので [Pa] に変換すると、ks=9.18 ×10-6 [cc/Pa] であり、Hyper2000 は Hyper1000 の差圧変換器に比べて約2倍 【硬い】 と言えます。水柱マノメーターと比べると、Hyper2000 は約1000倍の感度がある事になります。
果たして、差圧変換器の変位よる体積係数 ks がリーク検査の検出差圧 ΔP にどの程度影響があるかを確認します。(12)式において、
P = 大気圧 1.013×105 [Pa]
V1 = 100[cc] = 1×10-4 [m3 ]
ks = 5.24 ×10-12 [m3 /Pa]
k = 1
ΔV = 0.1[cc] = 1 ×10-7 [m3 ]
を代入すると、ΔP = 100.24 [Pa] という計算結果を得る。この時、
V1 = 1×10-4 [m3 ]
Pks(k+1) = 1.013×105 ×5.24 ×10-12 ×2 = 1.061×10-6 [m3 ]
である。従って、ks の影響は1%ぐらいです。しかしながら、測定圧力 P がゲージ圧力で 0.2 [Mpa] と高くなり、容積 V1 が1/3と少なくなると、3×3倍に影響が拡大することが読み取れる。従って、ks の影響は決して無視できないという結論となる。
(容積100cc以上、低圧(検査ゲージ圧 Pg ≦ 0.1 Mpa)時、影響2%以下となり無視しても大きな影響はない。)
③ Hyper2000の内部体積
Hyper2000 の内部体積は、コックを閉じたときのテスター内の容積 V0 であり、管路の体積計算と、実験から求めた数字です。検査ワーク側、マスター側とも同じ値です。
V0 = 6.70 [cc] = 6.70 ×10-6 [m3 ]
④ 外部容積(検査ワークと配管)の測定方法
検査ワークの体積、測定管路を含めたワーク側の全体積は、感度を比較する際、あるいはNG/OKの判定を決めるためには是非とも必要な数値になります。
4-1 可変容量マイクロメータを検査ワーク側の管路の途中に入れる。HPの写真のようにコックを介して取り付けると良い。厳密にはコックとマイクロメータの間に生じる体積を知る必要がある。
4-2 マスター側のコックを解放し、何も接続しない。これで、マスター側の圧力は大気圧となり、k = 0 として計算できる。ただし、外気に風があったり、ドアの開閉があったりすると、測定値に影響が出るので注意する必要がある。
4-3 マイクロメータを動かし、圧力上昇値と体積変化の関係を記録する。
マイクロメータの体積変化は、
ΔVm = 1.96 ×10-8 [m3 /mm] : 1mm 変位の時
4-4 マイクロメータが 1mm 前進したとき、ΔP = 31 [Pa] であったとすると、P は大気圧であるから、
= 1.013 ×105 ×6.268×10-10 = 6.35×10-5 [m3 ]
= 63.5 [cc]
として計算できる。
これは、49.5 [cc] のマスターチャンバーを接続したときの実験データと理論から計算した値であり、この時の配管容積は図面上で詳細に測定し結果 6.6 [cc] であった。
計算上の体積 V1 = 49.5 + 6.6 +6.7 = 62.8 [cc]
実験結果と理論計算値 V1 = 63.5 [cc]
となり、かなり正確に一致することが確かめられた。
⑤ 体積の違いと感度の比較
(12)式で、感度として支配的な項目だけで表現すると、

であり、同じ体積変化であるとすれば、その時の体積に逆比例して、圧力変化することが分かります。従って、ある組立完成品を構成する部品を検査する場合、その体積に差があるとすれば、体積の差を補正して、統一したNG/OKの判定基準を定めるのが望ましいと言えます。つまり、体積に応じたNG/OKの基準を考慮した上で、総合的に決めるべきであるのです。
6.検出圧力とリーク量
前項では、体積変化を与えたときの、感度・圧力変化を論じましたが、では実際にリークがあったときはどうなるのかを検証する必要があります。結論的には、前項の考え方を拡張すれば良いことが分かります。
① 検出圧力とリーク量の理論式
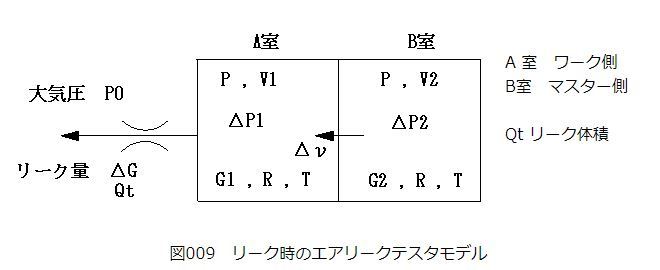
初期状態式
A室 PV1 = G1RT--------------------------------------(15)
B室 PV2 = G2RT------------------------------------- (16)
変化後の状態式
A室(P -ΔP1)(V1-Δν)= (G1-ΔG)RT-------(17)
B室(P-ΔP2)(V2+Δν)=G2RT-------(18)
その他の関係式
ΔP = ΔP1-ΔP2-------------------------------- (19)
k = V1/V2 = G1/G2-------------------------------- (20)
ΔGRT = P0・Qt-------------------------------- (21)
これを整理すると
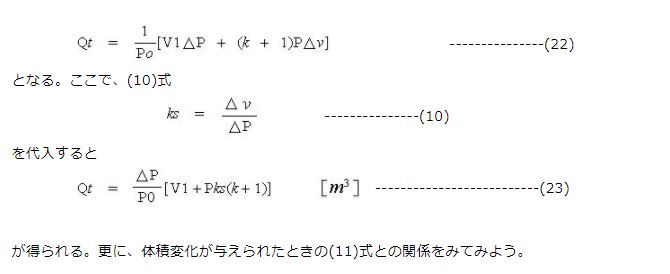
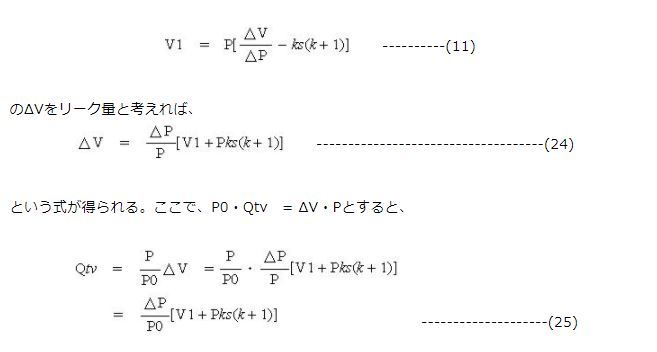
となり、(23)式と(25)式は同じになります。ここで、Qtv の方向と、ΔV の方向はリーク方向と反対方向ですが、両方にマイナスを付けても式は変化しません。つまり、図008 に示す ΔV を左方向に取り、増えた体積分の空気を外に放出したと考えれば、図009 に示すリークのモデルと同じになり、式も同じになるわけです。
従って、可変容量マイクロメータの容積変化を体積が増える方向に取ったとき、リークを擬似的に作ったと同じ事になります。実際は、体積が減る方向に取ったとしても、結果は同じになります。
リーク検査の場合、熱バランスを重視するため、マスター側と検査ワーク側の体積がほぼ等しくするケースが多いため、k =1 とすると、
ks = 5.24 ×10-12 [m3 /Pa]
P0 = 1.013×105 [Pa] 大気圧
P = P0 +Pg [Pa] Pg: ゲージ圧力 [Pa]
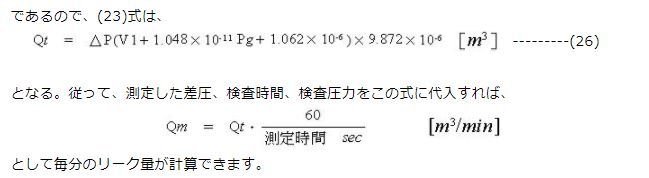
② 検査圧力と感度の関係

が導かれます。検査圧力と感度の関係を考えると、同じリーク穴であれば、検査圧力 P が高くなると、リーク量 Qt も増大します。そして(27)式の V1>>Pks(k+1) であるので、Qt にほぼ比例して ΔP も増大する。
しかし、経験的に検査圧力が高くなると、充填・平衡時間内における、空気の熱力学的状態変化が複雑になり、熱バランスが取りにくくなります。従って、測定値のバラツキが大きくなる傾向があり、安定した測定が難しくなります。
それ故、高い検査圧力が仕様として必要な場合を除き、適正な検査圧力を採用する方が良い結果を得ることができます。通常は0.2~0.3Mpaで測定する例が多いようです。